FaBrik - Wertstoffrückgewinnung aus metallhaltigen, staubförmigen Produktionsrückständen durch Faserabfall-basierte Brikettierung
In metallverarbeitenden Prozessen fallen wertvolle Abfallstoffe an, die bisher teuer entsorgt werden mussten. Im Projekt FaBrik werden aus Altkleidern recycelte Fasern genutzt, um diesen Metallabfall in Briketts für eine weitere Wertschöpfung zu binden.
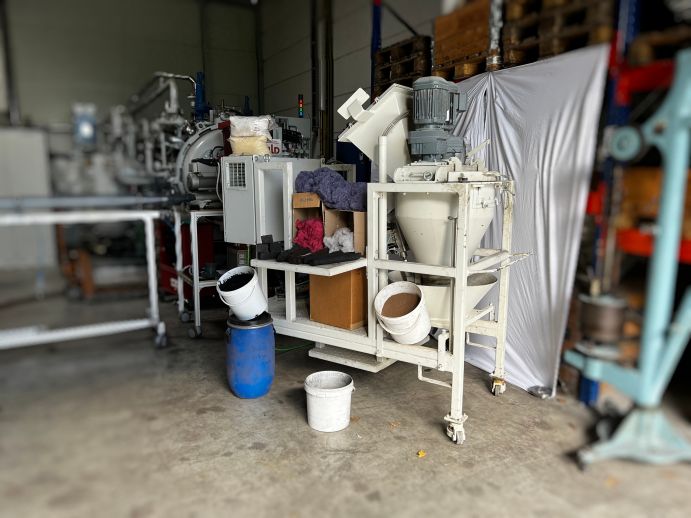
Aktuell liegen Prozessnebenprodukte (PNP) aus der metallverarbeitenden Industrie als Reststoffe vor, die in den meisten Fällen kostspielig entsorgt werden müssen. In den seltenen Fällen, in denen sie weiterverarbeitet werden, wird eine Mischung aus PNP, Wasser und Zement zu Briketts verpresst, wobei die Wasser-Zement-Mischung das Brikett zusammenhält. Diese konventionelle Bindung der Prozessnebenprodukte durch Wasser und Zement ist vergleichsweise kosten- sowie CO2-intensiv und kommt daher nur für sehr große Tonnagen (mehr als 35.000 Tonnen pro Jahr) in Frage.
Lösungen für die Weiterverarbeitung von Reststoffen: Projekt FaBrik kombiniert Restmaterialien
Im Projekt FaBrik ist untersucht worden, ob und wie Fasern, die nach dem Altkleiderrecycling nicht weiterverwendet werden können, zum Binden der PNP nutzbar sind, ähnlich wie in Faserverbundwerkstoffen. PNP und Faserabfälle waren bisher Prozessnebenprodukte, die schwer weiter zu verarbeiten sind, so dass ihre erfolgreiche Kombination und die Verknüpfung der jeweiligen Branchen einen großen Mehrwert bieten kann. Die fertigen Briketts können am Ende in der metallverarbeitenden Industrie weiterverwendet werden, um Rohstoffe daraus rückzugewinnen. Auf diese Weise wird eine weitere Wertschöpfung von Materialien erreicht, die zudem auch nicht mehr teuer entsorgt oder deponiert werden müssen.
Neue Wertschöpfung aus verschiedenen Abfallprodukten der Metallurgie und Textilbranche
Fasern zu Verstärkungszwecken zu nutzen, war bisher meist auf den Bereich der technischen Textilien begrenzt. Der innovative Charakter des Projektes FaBrik liegt also in der Anwendung von neuen Technologien, um damit Reststoffe aus zwei Branchen, wie Metallurgie und Textil, zu verarbeiten, die ohne dieses Projekt nicht miteinander kombiniert worden wären. Nach einer anfänglichen Recherchephase wurden im Projekt bisher ca. 15 Kilogramm an Einzelfasern aus Altkleidern produziert.
Untersuchungen zeigten hier die höchste Festigkeit bei Fasern aus Baumwolle (im Vergleich zu Polyester, Viskose und Gemischen). Mithilfe der von den Partnern weiterentwickelten und bereitgestellten Mischer und Extruder (Strangpressen) konnte mit einer Mischung aus diesen Fasern und PNP bereits ca. 300 Kilogramm Brikettmasse hergestellt werden. Im nächsten Schritt soll der erprobte Prozess in eine industrienahe Pilotanlage überführt werden.
Erkenntnisgewinn für eine nachhaltige Weiterverwertung von Produktionsresten
Ein bereits erreichtes Zwischenergebnis des Projektes sind fertige Briketts aus diversen, in Laborversuchen hergestellten Faser- und PNP-Mischungen. Nach ersten händischen Falltests wurde bereits jetzt von den späteren Anwendern bestätigt, dass diese Briketts in industriellen Prozessen gut weiterverwendet werden können, wie zum Beispiel im Hochofen bei der Roheisenherstellung. Dabei werden wertvollle Elemente wie Mangan, Eisen, Zink, Kalzium und Magnesium in den Prozess zurückgeführt und gleichzeitig die Energieeffizienz dieser Rückführung erhöht, da die so erzeugten Briketts nicht aufwändig getrocknet werden müssen.
Diese Erkenntnisse des Projekts zur Verarbeitung von aufgeschlossenen Fasern und PNP können auch in weiteren Branchen von Vorteil sein, da hiermit Abfälle in ihrer Menge reduziert und darüber hinaus einer weiteren Wertschöpfung zugeführt werden können.
Projektleitung
Anne Hennig
Institut für Textiltechnik der RWTH Aachen University
Otto-Blumenthal-Straße 1
52074 Aachen
Tel.: +49 241 80 23472
E-Mail: anne.hennig@ita.rwth-aachen.de
Zuletzt geändert am